Revealing Tomorrow's Potential: How Digital Twin Technology is Reshaping Our World
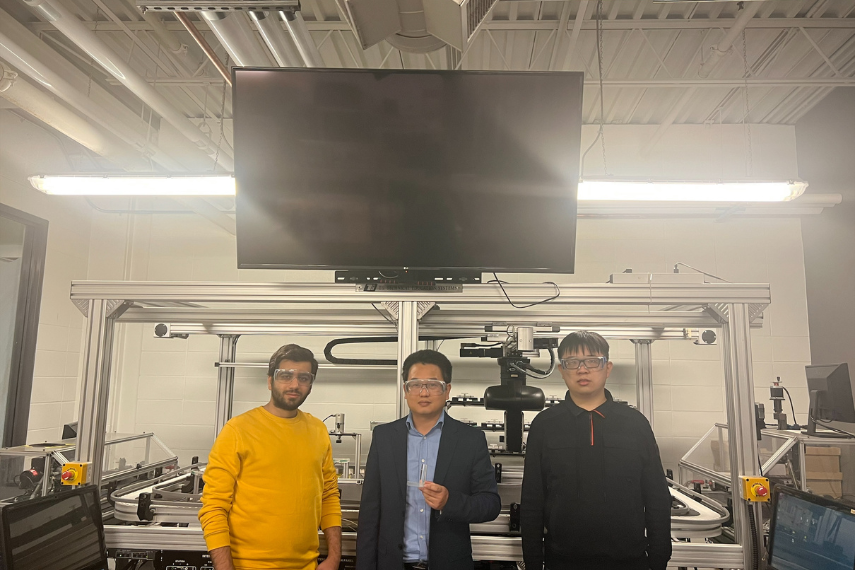
Digital Twin (DT) technology merges the real and virtual worlds, promising a future of smarter systems, innovative efficiency, and a transformed way of life.
Cloud-Based DT: Real-Time System Uprising
Step into the future with Cloud-based Digital Twin (CBDT), the cutting-edge technology where physical and virtual worlds unite. CBDT creates digital replicas of real-world systems in the cloud, allowing us to monitor, predict, and optimize their performance in real-time. CBDT is not just a technological advancement; it is a revolution in how we understand and optimize the world around us. It promises smarter, more efficient systems that adapt, learn, and evolve, shaping a future where precision, efficiency, and innovation go hand in hand to redefine the way we live, work, and thrive.
However, applying CBDT technology comes with its set of challenges. First of all, the scarcity of practical applications in complex systems leaves a gap between theory and implementation. The proprietary nature and high costs of specialized software further obstruct the accessibility of this technology, especially for smaller enterprises.
Pioneering CBDT Framework Showcase
Drs. Sheng Yang and Fantahun Defersha, from the School of Engineering, and their research team face these challenges head-on by proposing a comprehensive CBDT framework that integrates various physical and digital infrastructures. Their framework provides a practical demonstration by upgrading a legacy robotic assembly system, showcasing how CBDT can be applied in a real-world scenario, and not just theory.
The critical aspect lies in the demonstration of remote monitoring and control capabilities. By employing accessible tools and platforms like Google Cloud, the article avoids the traps of relying on expensive proprietary software. This choice not only makes the technology more inclusive but also showcases the feasibility of implementing CBDT without large financial investments.
Furthermore, the research emphasizes detailing the technical intricacies involved in creating a remote monitoring and control system. It delves deeply into the fundamental aspects of data acquisition for gathering information from physical systems or sensors, DT modelling for creating virtual replicas of real-world systems, simulation for simulating scenarios or processes based on collected data, and the Human-Machine Interface (HMI) which is an interface allowing interaction between humans and machines or systems. Indeed, it explains the core elements for anyone seeking to deploy comparable systems. It is not just theoretical; it is a tangible implementation showcasing the potential benefits of CBDT in revolutionizing manufacturing processes.
CBDT Future: Diverse Global Integration
Upon reflection on the research, Yang remarks, “The article lays a promising groundwork for future research in the field of CBDT technology. One path for exploration could involve refining the proposed framework by delving deeper into its integration with AI and digital technologies such as mixed reality across diverse industries beyond the scope of monitoring and control. This expansion could uncover new applications and opportunities for CBDT, potentially transforming sectors beyond manufacturing.”
Encouraging broader adoption and implementing standardized protocols could greatly boost CBDT's potential to become a fundamental component of the worldwide digital supply chain. A video showcasing the cloud-based digital twin platform for smart manufacturing is presented at the following link which provides detailed information about parts and operations: A cloud-based digital twin platform for remote monitoring and control
Funding Acknowledgement: This research is partially funded by the Natural Science and Engineering Research Council of Canada (NSERC) Discovery Grant, NSERC Alliance, Mitacs, and industrial partner – Aleo Canada
Reference: M. T. B. Touhid et al., “Building a cloud-based digital twin for remote monitoring and control of a robotic assembly system,” Int. J. Adv. Manuf. Technol., vol. 129, no. 9, pp. 4045–4057, Dec. 2023, doi: 10.1007/s00170-023-12611-7.